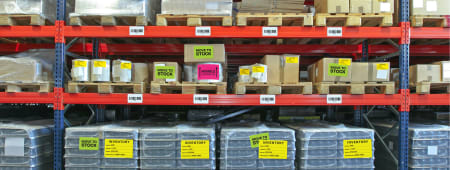
How to organize a warehouse for better efficiency
Proper warehouse storage organization is critical to maintaining a productive facility. Everything from how you receive inventory and stock products to how you retrieve and ship orders can affect the efficiency of your workers and facility. A well-organized warehouse allows you to carry out these tasks quicker, so your facility can operate more smoothly.
In this article, we’ll share our tips to not only organize your warehouse storage, but also increase overall efficiency. Even if you think your facility is running well, there’s always room for improvement. Help improve your operations by implementing these easy and useful warehouse and inventory storage ideas.
Shop Barcode & Warehouse Labels
Why you should organize your warehouse
The way you organize your warehouse can have a substantial impact on the productivity and efficiency of your operations. A cluttered and disorganized warehouse can cause a lot of needless problems. On the other hand, proper, well-organized warehouse storage can provide a wide range of benefits throughout your organization.
According to Jeff Havelka, Chief Executive Officer of Beyond Warehousing (a third-party logistics warehousing company), “a clean and organized warehouse encourages increased team productivity, leads to more efficient inventory management, eliminates waste, prevents health and safety issues, and represents company professionalism.”
Well-maintained warehouse and storage areas offer a more productive and safer environment for your workers. It saves time from having to look for items or move things out of the way and can help prevent time-eating traffic jams. The time saved means workers can pull materials faster and fulfill orders quicker.
Additionally, uncluttered shelves, aisles, and walkways help reduce the risk of accidents and injuries. A clean, well-ordered warehouse can lessen the chance of trips, slips, and falling objects. Providing an efficient and safe facility is great for improving worker morale, which can lead to an increase in customer satisfaction and eventual growth and expansion.
Best ways to easily organize warehouse storage
1) Clear the clutter with 5S/6S
Clutter is a common occurrence in any warehouse, so it’s important to set aside time to clear any buildup. “Removing clutter enables companies to take full advantage of their warehouse’s valuable spaces,” Havelka advises. It’s good to conduct cleanups throughout the year in order to ensure everything is running as smoothly as possible. However, try to schedule them during your slower times so it’s easier to keep your inventory stored efficiently.
A good starting point when it comes to clearing out the clutter is to go back to the basics of 5S/6S principles and other lean manufacturing concepts. This will allow you to focus on eliminating waste while maximizing efficiency and productivity. Learn more about the 5S/6S methodology and the benefits of each principle to optimize your organizing process.
Regular use of lean strategies can lead to increased productivity, higher product quality, reduced costs, and a safer work environment. It will also help create sustainability for your operations, allowing you to be better equipped for future growth.
2) Review your warehouse layout for hidden opportunities
Now that you’ve cleaned up the clutter and removed excess inventory, supplies, tools, and equipment, you can better optimize your warehouse space. Instead of expanding the footprint of your warehouse, reorganize your warehouse layout to make the most of the space in terms of efficiency and storage.
Here are some great warehouse strategies for optimizing storage space:
- Take advantage of vertical space. Use stacking bins with durable ID labels to keep things organized vertically.
- Reduce empty rack space by standardizing bins to fit the rack height.
- Identify underutilized space. For example, is there room for hanging shelves above a conveyor belt or adding a storage trailer in your lot for seasonal supplies?
- Create simple, clear paths for foot traffic and forklifts. This will help prevent accidents and minimize the number of steps your workers take for each order.
- Reduce travel time by making the most-picked items more accessible. Store items frequently sold together near one another and high-volume items near the front of the warehouse.
- Post clear, easy-to-read signs to better guide workers and visitors to where they need to go. Find the best tools for creating onsite signs and labels on our helpful resource page.

3) Streamline with warehouse management system software
Take the time to consider implementing or upgrading your warehouse management software (WMS). There’s plenty of time and cash flow to put towards optimizing warehouse efficiency by determining the most effective use of both space and labor using WMS.
For example, as you re-evaluate your warehouse layout, WMS can help you determine material, product, and equipment locations that optimize the flow of your warehouse. WMS can also suggest the best routes and methods for picking or putting away.
You can also use asset management software like Reftab to help keep track of your warehouse equipment. Improving the way you manage your equipment can help you save time, improve workflow, track accountability, and keep things organized.
4) Increase mobility with smartphones & tablets
There are pros and cons for using radio frequency scanners (RF guns) versus smartphones or tablets in heavy-duty environments like warehouses. While many argue RF guns versus smartphones as “either or,” in reality, a combination of the two is likely to be the case in terms of increasing warehouse efficiency.
For example, RF guns are typically better for long-range scanning and are inherently more durable. As you optimize your warehouse layout by increasing the use of vertical space, RF guns are extremely handy. On the other hand, smartphones and tablets often require less training and can work as mobile workstations for warehouse managers and other employees.
WiFi-enabled smartphones and tablets with durable cases provide warehouse managers and employees with a constant connection to inventory or warehouse management systems. No more heading back to the office for printed reports, data is accessible anytime and anywhere.

5) Update barcode labels to improve inventory management
Barcode labels allow workers to gather and store data quicker and more accurately than manually recording it. However, incomplete or incorrect scans from damaged or hard-to-reach barcodes can slow down productivity and disrupt warehouse efficiency and workflow. For this reason, we devoted an entire article to showing you how to get started with barcodes.
Old peeling or taped-over labels should be replaced with durable barcode labels that are engineered for long-lasting performance in heavy-duty environments. Labels for hard-to-reach or vertical storage areas should be replaced with high-visibility labels, like our reflective barcode labels that feature a retro-reflective finish for creating long-range barcodes that can be scanned from a distance.
If you’ve already integrated mobile devices into your warehouse operations, you might consider switching to or adding QR codes in certain areas. Not only do QR codes hold much more information, but they are also able to integrate seamlessly with camera-operated scanning on devices (versus scanning via reflected light).
6) Review and update your picking process
There are many picking processes to choose from including, single order, zone, batch and wave picking; what method works best really depends on the facility and is likely to change over time. Review your picking process and look for ways to make things more efficient.
For example, one way to make it easier for workers to spot items is by using bright, easy-to-see labels. We recommend our assorted neon labels. The attention-grabbing colors make the labels stand out from any distance, and the permanent adhesive provides a long-lasting hold.
As mentioned, reflective barcode labels can help with inventory management, but they can also help avoid picking errors by improving the label’s visibility in low-light situations. Minimizing errors reduces order mistakes and improves customer satisfaction. Learn more about creating reflective sign labels by watching the video below.
Ensuring all picking equipment is well maintained is also important. Schedule frequent evaluations and checks of equipment and ask workers to report problems immediately. Regular maintenance and care can help prevent equipment breakdowns, which will take extra time, manpower, and money to fix.
Your pick lists should also be reviewed. Make sure you use well-organized lists in a logical pattern. When workers fulfill orders, they should pick up everything they need as they pass instead of going back and forth between areas.
7) Continually look for ways to improve
Our last warehouse storage tip is to always think of organization as an ongoing process. Make organizing a continuous procedure for finding and implementing improvements to your operations. Your business will continually change and grow as time goes on, so don’t stop looking for ways to improve.
Using our organization tips is a great starting point, but keep the future of your business in mind. Ensure your warehouse is adaptable to changes and eventual expansion. Storage solutions for your current inventory may be working perfectly now, but you never know what the future holds.
The Takeaway
The benefits of proper warehouse organization are too good to pass up. Improved efficiency and productivity, a safe and healthy work environment, and improved customer satisfaction is worth the time and energy it takes to keep your warehouse and storage areas clean, uncluttered, and well-organized.
Hopefully these tips can help you create an organization process that works for your warehouse, so your facility can reap the benefits for years to come.
To learn more about organizing your warehouse using 5S/6S principles, check out our free whitepaper with 5S/6S labeling solutions.
Please note, the contents of this article and related articles on avery.com/industrial are for informational purposes only, are general in nature, and are not intended to and should not be relied upon or construed as a legal opinion or legal advice regarding any specific issue or factual circumstance.