3 Ways PPE Asset Tags Keep an Eye on Gear
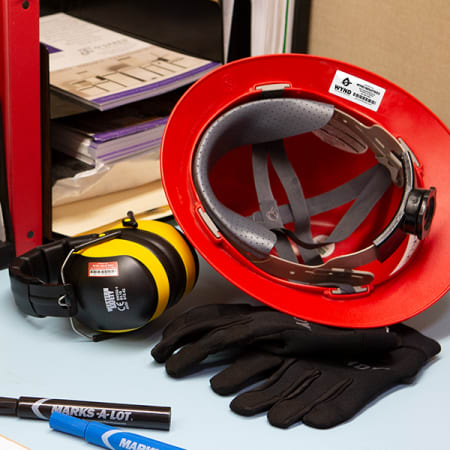
What is PPE?
PPE stands for personal protective equipment. OSHA standard 1910.132 covers PPE requirements for protecting workers from hazards on the job, as well as defining the role of employers when it comes to providing personal protection for employees.
In a full 48-page publication and additional supplemental PPE resources, OSHA provides further context for employer responsibilities regarding various types of personal safety equipment. It can be helpful to think of PPE divided into three categories:
- OSHA-mandated long-term equipment. This can include items like metatarsal foot protection, prescription lenses for full face respirators, earmuffs, hard hats and face shields.
- OSHA-mandated single-use disposable items such as earplugs or latex gloves.
- Personal items that are exempt under the OSHA rule such as non-specialty steel-toe boots and ordinary weather protection such as a parka or sunscreen.
How to Use PPE Asset Tags in Your Facility
In general, asset tracking is the system of managing how a business’ valuable items are audited, tracked, repaired and protected. Most people are familiar with the security asset tags on computers and other expensive electronic devices used for IT asset tracking.
Did you know you can also use asset tags to help you meet PPE safety and compliance goals? Promote a safer workplace and streamline resources spent on your PPE program by using PPE asset tags to track long-term personal protection items mandated by OSHA.
Digitally tracking personal protection gear using PPE asset tags with barcodes is much quicker and more accurate than manual data entry. A barcode on a PPE asset tag can be scanned in mere seconds, updating a centralized database with no need to transfer written information to devices or digital data between files.
1) Protect expensive safety equipment with PPE asset tags
It’s true that an asset tag can’t physically stop an employee from walking away with company-issued property. However, PPE asset tags make it easier to identify missing items faster and trace them back to the person responsible for the item.
When PPE is not regularly accounted for, it’s extremely easy for lost and stolen equipment to go unnoticed and/or unreported. Just having a system in place for regularly auditing PPE communicates that employees will be held accountable for assigned equipment.
Accountability can be an effective theft deterrence and also encourage employees to be more careful with valuable safety equipment.
2) Use PPE asset tags to help safety officers comply with requirements
A centralized digital database for PPE places important information at your fingertips. OSHA regulations as well as in-house and employee union requirements stored in a digital PPE database can easily be accessed and updated by scanning PPE asset tags.
Safety officers can quickly and easily get a complete overview of all company PPE, to whom it’s assigned and what activities require its use. Better access to more reliable data makes it easier to review, update and evaluate PPE programs.
Even on a micro, day-to-day level, PPE asset tags help safety officers and PPE managers fulfill requirements more efficiently. Imagine you’ve got a new worker joining your construction crew or an employee switching departments.
Wouldn’t it be great to quickly and easily check what safety equipment you already have on hand before ordering new gear? Or quickly view what new equipment is needed and what should be returned as workers move from different activities?
When digital records are well maintained, there’s no need to rush to a warehouse to physically count equipment or scramble to look up individual PPE requirements.
3) PPE asset tags can track the life span of personal protective equipment
PPE has a finite life span and must be periodically renewed or replaced. Replacement reminders, warranty expiration dates and other pertinent information can also be added to your database using PPE asset tags.
Many asset tracking programs have options for setting alerts and reminders and/or the capability of linking to digital calendars. For example, if a piece of PPE should be replaced after six months, you can set automatic reminders for both employees’ and manager’s calendars six months from the issue date.
Likewise, PPE asset tracking can help alert safety officers and PPE managers in advance of warranty expiration dates. Using PPE asset tags to track equipment this way allows your team to renew or replace warranties leaving no gap in coverage.
Of course, these types of long-term reminders don’t replace regular PPE inspection because safety equipment should always be checked before and after each use. Nor do they replace regular PPE maintenance requirements such as cleaning, storage and what to do with broken or damaged items.
However, PPE asset tags do make it easier for employees to record/report any PPE issues they may discover upon inspection. General asset tracking benefits include increasing maintenance efficiency by keeping better MRO records. Likewise, PPE asset tags make it easy to quickly record damaged safety equipment and remove them from ready-to-use PPE inventory.
How to Choose the Right Materials for PPE Asset Tags
Personal protection equipment is generally exposed to heavy-duty use and/or demanding environments. Standard paper labels for the office simply will not meet the challenge. To make sure your PPE asset tags last the entire life span of your gear, it’s important to choose durable labels designed for industrial use.
The best material for PPE asset tags is a durable aluminum-fortified PET film with Industrial-grade, strong adhesive. Material durability and strong adhesive are absolutely crucial to ensure your PPE asset tags won’t degrade in heavy-duty environments.
Torn, scratched or otherwise damaged label surfaces, as well as dirt and other build up can result in incomplete or incorrect barcode scans. PPE asset tag material that’s waterproof as well as abrasion, chemical and tear-resistant helps preserve the scan quality of barcodes.
Quick PPE Asset Tag Material Checklist
- Aluminum-fortified PET film
- Strong industrial-grade adhesive
- Abrasion and tear resistant
- Waterproof, chemical resistant
Flexible PPE Asset Tag Solutions
Creating your own asset tags is easier than you might think. Printable label innovations have made it possible to print custom labels on industrial heavy-duty materials right in your own facility— no need for expensive specialty printers and barcode generator software.
All you need to create your own PPE asset tags is a laser printer, printable durable asset tags and online label design software that includes a barcode generator. Label suppliers that offer low or no-cost software options greatly reduce the startup costs of implementing PPE asset tags in your facility.
As your PPE tracking demands grow, low-minimum custom printing services is a great way to scale up to fit your needs. Label suppliers with integrated professional printing services make it easy to transition from printing PPE asset tags on site to custom printing and vice versa.
Whether you need the speed of on-demand printing or several thousand PPE asset tags, there’s a PPE asset tag solution out there that fits your facility.